GREENSHOT
A PERMANENT AND AUTOMATED FLUID LEVEL SYSTEM
KEY OUTPUTS:
- 144 Pressure Build Ups Per Day
- 1-10 fluid levels per day
- 1 Acoustic Velocity Shot Per Week
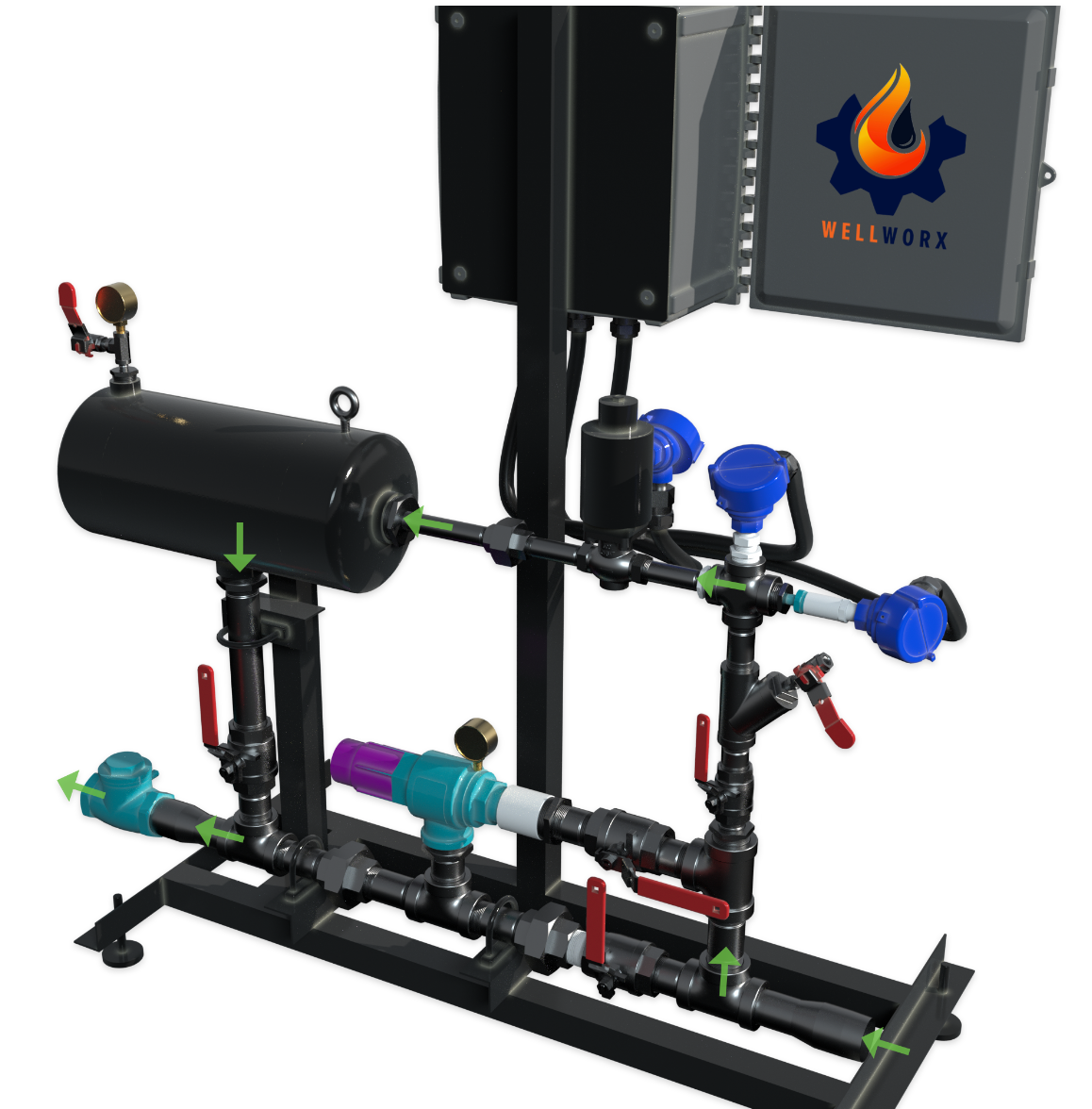
The First of its Kind – Worldwide
The GREENSHOT brings Frequency, Accuracy and Consistency to ESP and Rod Pump Applications. It shoots 1-10 Fluid Levels per day, one Acoustic Velocity Shot per week and 144 Pressure Buildups per day. It’s also the ONLY permanent and automated fluid level system that is truly ‘green.’ The system functions without high-pressure nitrogen or CO2 and all actions performed by GreenShot utilize the well’s naturally-produced casing gas.
Consistent Reservoir Data in an Inconsistent World
With each Fluid Level Shot, GREENSHOT provides the end user with SEVEN key data points:
- Fluid Level Above Pump (FLAP)
- Gas-Free Fluid Level Above Pump (GFFLAP)
- Acoustic Velocity (AV)
- Pump Intake Pressure (PIP)
- Casing Pressure (CP)
- Fluid Gradient (FG)
- Casing Gas Produced Up Casing in Thousand Cubic Feet per Day (mcf/d) (CGP)
FLAP
5,172 ft
GFFLAP
AV
PIP
CP
FG
CGP
7 Key Data Points That Will Change the Industry
- 6,334 ft | FLAP
- 5,172 ft | GFFLAP
- 1,200 ft/s | AV
- 1,958 psi | PIP
- 94 psi | CP
- 0.295 psi/ft | FG
- 16.117 mcdd | CGP
Cloud-Based Technology
All data collected by GREENSHOT is stored and accessed at the user’s convenience using the cloud-based GREENSHOT User Interface. Our interface allows users to shoot fluid levels, pressure buildups and acoustic velocity shots on the fly. This interface is providing the reservoir and dh data sets that have been missing in our industry for years in an accurate manner, without the use of dh gauges.
- Fluid Level and Pressure Build Up’s on demand and at your fingertips!
- Data is uploaded instantaneously using cloud-based technology.
- Access anywhere with the GREENSHOT User Interface.
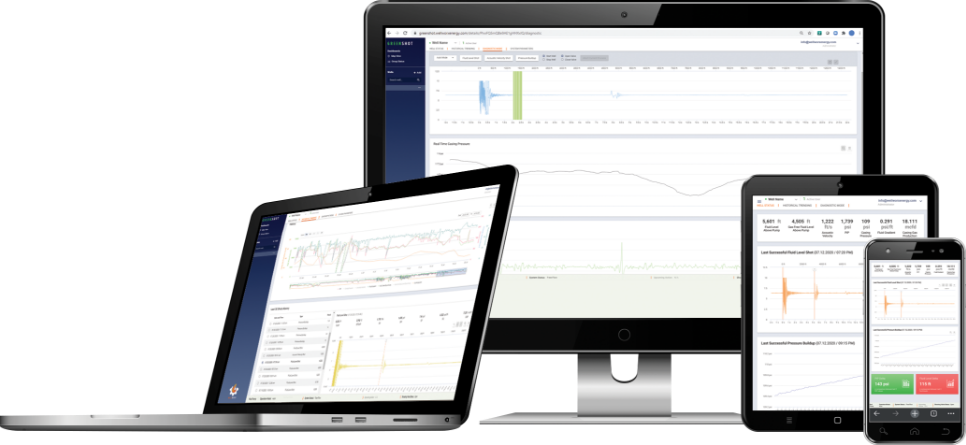
How it Worx: A Step-By-Step Guide
Green Energy
GREENSHOT shoots Pressure Build Ups, Acoustic Velocity Shots and Fluid Level Shots through the closure of a Shooting Valve that separates the flowline and casing line. As the pressure differential across this valve is built, a delta is created; the larger the delta, the larger the “shot.” These shots utilize the wells produced casing gas to create the pressure differential. No foreign matter is introduced to the reservoir or leaked to the atmosphere.
Acoustic Technology
Once the desired delta is achieved, the Shooting Valve is cycled rapidly. The energy created is amplified through the surge tank, creating the shot. The Acoustic Transducer and GREENSHOT Sensor assemblies are used in unison to monitor the round trip of this shot from the fluid level back to the well surface.
Round Trip
The time needed to complete the round trip of the shot is monitored and recorded. Once the round trip is complete and all data recorded, the Shooting Valve returns to its normally open state and free flow of the well resumes. This process is repeated throughout the day at various durations and with various pressure deltas to achieve Fluid Level Shots, Acoustic Velocity Shots and Pressure Buildups.
What Can This Data Provide?
Today’s Challenges
- Understanding today’s wells requires more data than a traditional Downhole Card provides alone.
- Periodic fluid levels and pressure buildups do not provide reliable fluid level data sets in today’s dynamic production climates.
- Accurate reservoir data is extremely difficult to gauge without costly and short-lived DH Sensors.
- Fluid Gradient is not available in any system currently, making BHA and Pump Efficiencies difficult to trust.
- Design efficiencies are often limited due to poor data available at time of design.
- High Pressure CO2 and Nitrogen prove to be unsafe, costly and do not fit the Green initiatives sought in today’s energy-conscious environment.
GreenShot Opportunity
- Enhanced well optimization practices.
- Perform 144 pressure buildups daily, which allows for constant monitoring of dynamic gas production incasing.
- With accurate and real time PIP, operators can confidently consider running artificial lift systems more aggressively than before.
- Quicker detection of poor well performance by viewing PIP and FL Delta’s between shots.
- Quicker detection of frac communications when PIP is viewed from a field-wide level.
- With PIP and Fluid Level information, accurate Fluid Gradients can now be measured and trended overtime.
- Identify better artificial lift design practices utilizing PIP Trends
– Come off ESP quicker with larger rod pump systems?
– Run ESP Systems longer due to increased dynamics seen in rod pump applications throughout field
Three Basic Functions
For the highest accuracies, it is recommended that the user allows one 24-hour period for all gas-production data to be normalized. The accuracy and frequency of this data is what allows the GreenShot to provide its three basic functions:
Gas production data is gathered through the casing without measuring it with a standard orifice meter.
This is done periodically via GreenShot’s 144 Pressure Buildups per Day by measuring in intervals of one minute. The natural gas that travels through the device during the 10-minute period is calculated using a formula based on real gas laws. The incremental rates are summed using the Trapezoid Rule. Essentially, the daily casing rate measured in thousands of cubic feet per day (mcf/d) is known. Producers have historically not been willing to invest in orifice meters to measure casing gas. With the GreenShot, it is now possible to do that as part of a multi-purpose device, adding value to the well.
The GreenShot shoots daily automatic fluid levels using the well’s produced casing gas in a closed system.
The method is acoustic and “green” in that nothing foreign is emitted or injected into the well to create the acoustic wave. This key feature allows producers to limit the amount of greenhouse gases released to the atmosphere during production and recovery. The fluid level is used to compute parameters that indicate each individual well’s production potential. Pump Intake Pressure (PIP) has traditionally been a difficult data set to accurately acquire outside of Electrical Submersible Pump (ESP) wells with working downhole gauges. The importance of an accurate PIP cannot be understated, as it weighs heavily on optimization and well design decisions. If the PIP is high, more production is likely available. If the PIP is low, the well is likely producing at capacity at the pump’s present setting depth. Additionally, subtle changes in acoustic velocity are thought to accompany production changes from zone-to-zone in multiple-completion wells.
The GreenShot records are combined with results from the pump-off controller to provide continuous well tests.
Using the downhole pump as a meter, the pump-off controller estimates the amount of oil, water and gas that are produced through the tubing. The GreenShot estimates gas produced through the casing. The combination of data creates a complete view of the total production stream, which is instrumental in maintaining maximum production. Malfunctions can be identified sooner, remedial action taken immediately and production allocated between wells producing into the same tank battery. This information, gathered with no human effort, is useful to reservoir engineers in preparing oil and gas reserve reports for management and stockholders.
Rod Pumping: Principles, Best Practices and Technologies
Registration is now open for individuals and/or teams and training is scheduled quarterly.
Sign up for email updates!